The impact of using an FAA STC for ADS-B Pairing approvals
Rick Ochs • July 29, 2020
ADS-B Beyond 2020
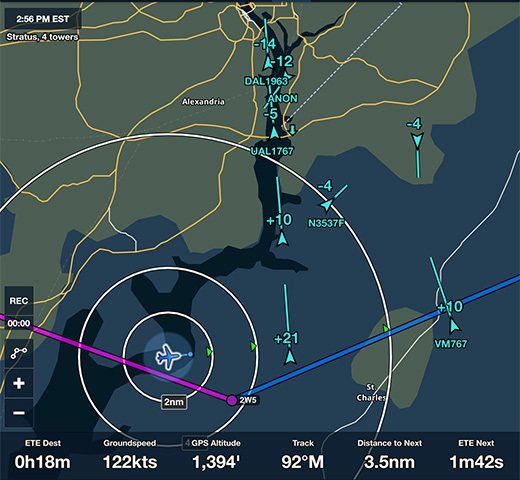
The problem has always been, this pairing specification is highly defined and is now locked in state due to product part numbers tied to the STC by the FAA thru its approval of the ADS-B installation via an STC.
The current failure rates of installed system validates that ADS-B installations are being accomplished without proper test equipment and specially trained technicians involved.
- Rick Ochs, CEO
Through a myriad of requirements driven by an Advisory Circular, the Federal Aviation Administration (FAA) deemed that all ADS-B installations can only be qualified using an FAA approved Type Certificate, an Amended Type Certificate or a Supplemental Type Certificate (STC) process. This process is used to validate the equipment pairing of an ADS-B compliant Transponder & WAAS GPS sensor to make up an approved ADS-B solution. This STC may then be applied to any number of aircraft that can utilize the component pairing defined in the STC to qualify as a new, FAA approved ADS-B compliance solution for the aircraft owner.
Currently, the failure rate of ADS-B equipped aircraft is over 9% as averaged over all aircraft in US domestic service for the first 6 months of 2020. This measure is drawn directly from the FAA website for current US equipage levels of ADS-B compliant aircraft. This exceptionally high average failure rate is derived from the difference between “Good Installs” and “Non-Performing Emitters”. According to the FAA, these failures are almost exclusively a result of ADS-B system misconfigurations deemed as “Installation Errors” and not Transponder or WAAS GPS equipment failures. Rarely, if ever is the ADS-B failure alerted to the pilot via the newly install ADS-F Fail annunciator that drives the need for a new Airplane Flight Manual Supplement.
An ADS-B STC project Safety Analysis requires a reliability factor of 10 to the negative 9th power to gain FAA approval. Systematically, ADS-B as deployed is operating at 10 to the negative 1st power. If this were any other systematic failure with such highly defined causes, the Airworthiness Directives would be flying out of D.C. to address and resolve it. This problem is rarely acknowledged for the scale of it and nothing has been discussed or offered to get it quickly resolved by the FAA. We need to know why it is happening and what more needs to be done to resolve it.
I believe that a major cause of ADS-B system misconfigurations are driven by the STC. Avionics installers working on an ADS-B project that have an STC data package in front of them, may be mostly referring to it though it was developed for an entirely different aircraft. The configuration settings may be wholly different than what is required for the new installation. If there may be questions on a setting, the installer may be using what is believed to be an FAA approval to set ADS-B parameters that are likely erroneous to configure the new installation.
Installers must have the proper training and test equipment and internal processes to validate and record the proper operation and configuration settings to authorize the ADS-B system operations. ADS-B installations by their nature integrate with the very systems as identified in FAR 91.413 and FAR 43 Appendix F. With that, ADS-B installations MUST only be accomplished and the aircraft approved for Return to Service by an appropriately rated FAA certified Repair Station.
Any installation approved by an Inspection Authorized Airframe & Powerplant Mechanic (IA) cannot be deemed legal and should always be highly discouraged. Suggesting an IA do an ADS-B installation and then the aircraft should go to a Repair Station for final airworthiness signoff is unwise, uncommon and useless as a suggested path for an aircraft owner.
Many challenges exist with the current ADS-B airworthiness certification path. This “Pairing” must be approved via STC with very few other alternatives for ADS-B system installation approval. There has never been such a certification scheme by the FAA to Supplement something that was never Type Certified to begin with (as far as I can tell). This fact presents unforeseen challenges.
Normally, an STC is applicable to a Type Certification of an actual aircraft. In the case of ADS-B, a pairing is used as a basis for an STC project though a real aircraft is identified as the engineering baseline in the certification plan to administer the STC. All engineering and testing now involved with the installation becomes a part of the STC. Much or very little of the STC can then be applied to any number of aircraft that can use that same Transponder/WAAS GPS electrical pairing to gain ADS-B compliance.
The problem has always been, this pairing technical specification is highly defined and is now locked in state due by the FAA thru its approval of the ADS-B installation via an STC. There can be no software or hardware changes to either device throughout the life of the applicable pairing STC without subsequent engineering reviews, TESTING and FAA approvals of amended STC’s.
It is inevitable that through s short span of time, the STC will need to be amended or replaced with an entirely new STC. This is due to the reality of software or hardware changes that occur with a modification to either paired device that happen as OEM manufacturing processes mandate. These firmware changes are a normal function of product improvement in a manufacturing environment. These modifications may or may not involve a unit part number change.
Such as the case with a WAAS GPS sensor that has recently been deemed to have a software bug that was not discovered when it was built and certified for approved WAAS GPS LPV approach operations along with ADS-B capabilities. The same GPS is used for both navigation and ADS-B position reporting. This software bug can only be resolved with a major software change and a part number roll to a new part number of the same model number WAAS GPS. Though not required for ADS-B continued airworthiness, that change will now affect every single jet in operation that has already been upgraded to these WAAS GPS units for ADS-B compliance. Should it require service, it will come back with a different part number from an OEM repair.
The worst time to find out about a different part number provided to replace a failed unit is when the time comes for a proper logbook entry to sign off what should be a routine ADS-B maintenance event. No alternative part numbers or software changes have been approved under the ADS-B STC used for compliance that is now in jeopardy as the failed part number unit is no longer readily available. Any new or exchange/overhauled unit from the OEM will come with the new firmware change due to manufacturing quality assurance processes. A quick turn maintenance event to get a working aircraft back in service is not to find out that a new STC is now required due to parts obsolescence driven by product improvement processes.
Anytime a GPS or transponder is sent into the OEM for any repairs, it may come back with a different software level or hardware part number. This action will deem it to be unacceptable for reinstallation in the aircraft that it was removed from. This is because the repaired unit, with a different software or part number will no longer comply with the STC that it was originally certified to for the aircraft undergoing ADS-B maintenance. There can be no deviations for future enhancements to the approved pairing that makes up the ADS-B source equipment without the STC being amended or replaced with a new STC.
If we are going to be honest about it, in such a simple STC that exists primarily for the digital databus pairing of 2 discrete components which may be different product OEM’s, any and all software or firmware change is a major change to the STC. That means a new STC is in order as an amendment is not recognized for an STC application to make any product improvement changes.
Additionally, if the ADS-B component manufacturer is not the owner of the STC as utilized for the ADS-B installation, the “3rd party STC Holder” may not / will not amend or replace their previous STC to maintain current airworthiness standards of any aircraft affected. An aircraft that is AOG for ADS-B will suffer significantly in need of a new airworthiness path for what should be a normal maintenance event. This is a major problem now for many in the avionics and MRO community that service ADS-B systems.
My idea for a solution is also a great attribute for repair stations that spend so much time, heart and intellect supporting the continuous FAA oversight and approval of aircraft Return to Service processes. An ADS-B installation should be considered a Major aircraft alteration yet not a major change to the Type Design for any aircraft. (If the same WAAS GPS is used as a navigation source, this is an entirely different topic relative that that system’s ongoing airworthiness approvals.)
The FAA should grant privileges to Repair Stations to install and recertify ADS-B system installations per under new Operations Specifications. Return to Service approvals for ADS-B systems using normal requirements of proper tooling, training, personnel and facilities and a Quality Controlled process as required under FAR 145 should be perfectly leveraged to provide this needed service. This is a simple plan and it will effectively address the current extraordinary in-service failure rates of deployed ADS-B systems.
The FAA should certainly enable Repair Stations actual privileges for ADS-B installations with full system integration validations and Return to Service airworthiness certifications. The current failure rates of installed systems validates that ADS-B installations should not be accomplished without proper test equipment and specially trained avionics technicians involved. FAR regulations have made clear for decades that any Transponder or altitude encoding system maintenance must be done by an appropriately rated & certified Repair Station. All 1090 ADS-B Out upgrades involve these systems along with the majority of 973MHz UAT systems.
Through 14 CFR, FAR 145 approved Repair Station Operations Specifications, ADS-B system integration, installation and testing along with an affirmative Public ADS-B Performance Report from the FAA ADS-B website should form the basis of the proper continued airworthiness needs of ADS-B system integration. This is no different than Transponder and Altimetry systems are maintained today.
As an example of previous FAA airworthiness approval processing, GPS navigation receivers in aircraft used to require an STC for IFR approach capability approvals when they were considered new and novel. The FAA provided installation approval policy to enable a VFR only installation until such time a test flight was flown consisting of 3 successful GPS approaches and a defined error parameter worksheet was completed that was made a part of any applicable GPS IFR work order. Once the test flight was completed, another FAA Form 337 was completed, an Airplane Flight Manual Supplement was incorporated into the aircraft documents, and the aircraft was approved for IFR operations as noted by a new placard stuck to the instrument panel.
This plan will better leverage Repair Stations to eliminate the excessive failures rates of all ADS-B equipped aircraft in the ATC system today. It is a common-sense approach to ADS-B system reliability and the ever-evolving ongoing maintenance requirements for NextGen operations.
BLOGS
The Impact of Using FAA STC's for ADS-B
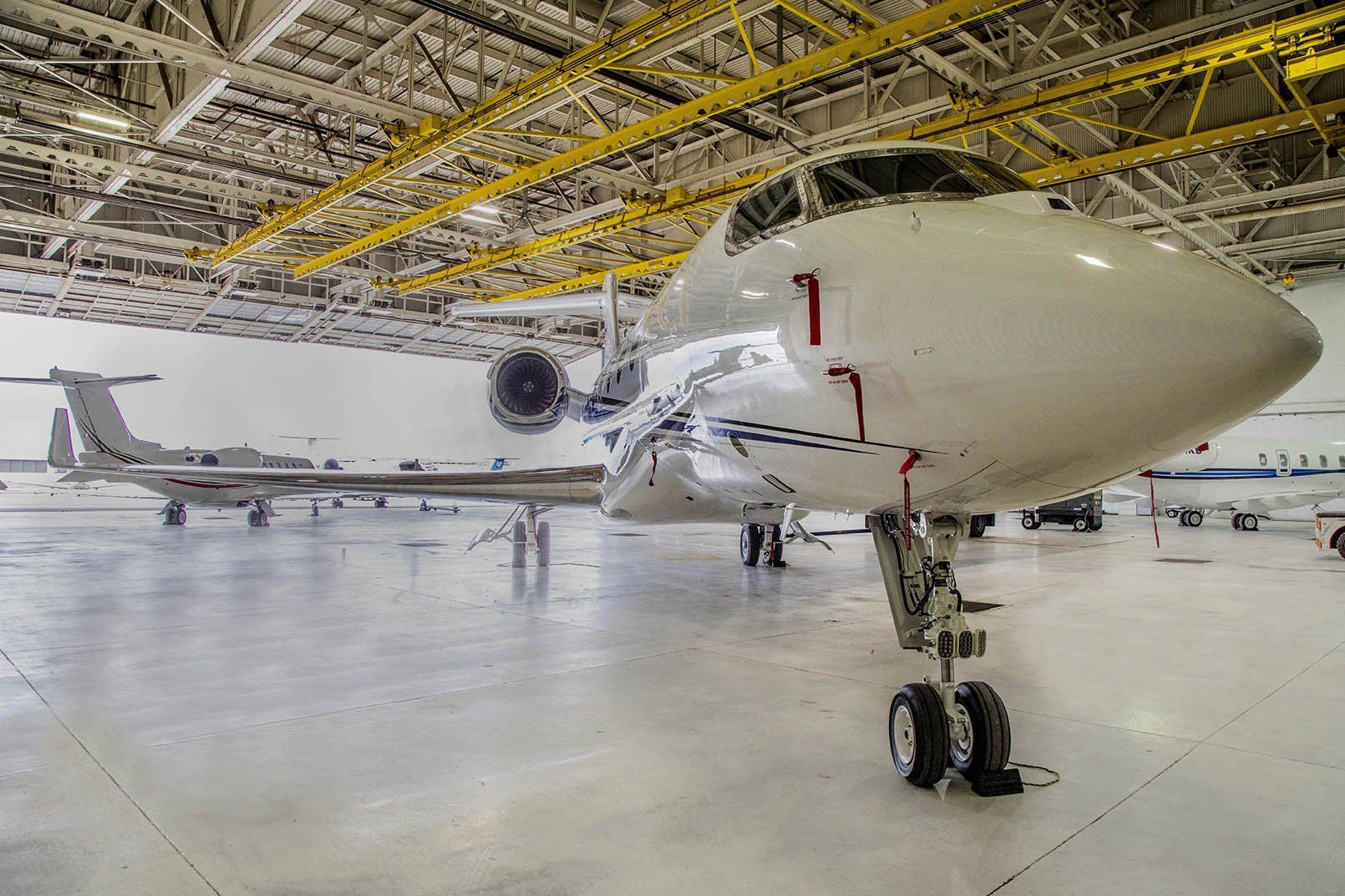
The way Rick Ochs sees it, there are lots of advantages to being a relatively small avionics company serving business aircraft owners and operators. For starters, there’s the ability of his company—Spirit Aeronautics—to provide customers with personalized services and solutions tailored to their needs.